Smart Bubble System: Campus Technik Lienz und testtec GmbH initiieren Bahnbrechendes
Mechatroniker des Campus Technik Lienz und der testtec GmbH haben eine entscheidende Grundlage für die Entwicklung leichterer, energieeffizienterer Getriebeölpumpen gelegt.
Ein internationales Privatkonsortium unter der Führung des Campus Technik Lienz (Division für Mechatronik) und des Prüfstandstechnik-Spezialisten testtec GmbH haben eine Innovation vorgelegt, mit der ein lange Zeit ungelöstes Problem der Autozulieferindustrie gelöst werden kann. Das bei allen Automarken einsetzbare Smart Bubble System stellt Luftblasen im Öl mit exakter Größenverteilung in Echtzeit dar. Herkömmliche Systeme am Prüfstand können zwar den prozentualen Luftgehalt der Blasen bestimmen, jedoch nicht ihre Größe und Verteilung. „Es macht einen Unterschied, ob eine große Luftblase zur Pumpe kommt, die das Potenzial hat, viel Schaden anzurichten, oder viele kleine, die einfach abprallen“, erklärt der wissenschaftliche Leiter der Division für Mechatronik, a.o. Univ.-Prof. DDI Dr. Fadi Dohnal.
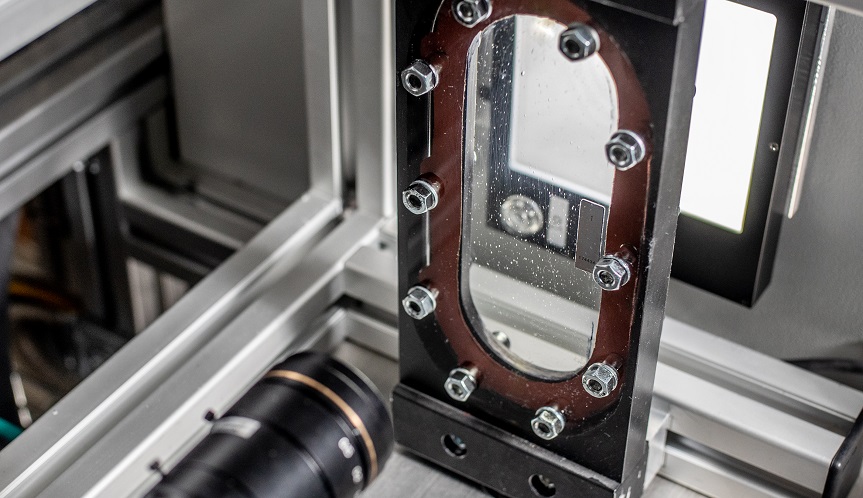
Optische Messeinheit (Luftblasenmessung in Echtzeit) am Prüfstand. Die Luftblasen werden durch ein Sichtfenster gequetscht.
Blasen im Öl: überdimensionierte Bauweise von Ölpumpen sorgt für mehr CO2-Ausstoß als nötig wäre
Luftblasen entstehen, wenn Verschmutzungen im Öl zu Abrieb in der Pumpe führen. Die Folge sind Materialschäden, welche die Pumpe und im schlimmsten Fall auch das Getriebe selbst zerstören können. „Das Öl im Ölkreislauf von Fahrzeugen wird durch die hydraulischen Kupplungen, Wandler etc. stark beansprucht und somit auch verschäumt“, so Dohnal. Um Schäden möglichst hintanzuhalten, werden Ölpumpen überdimensioniert konstruiert – nach dem Prinzip: je massiver die Bauweise, desto weniger „kaputtbar“ ist die Pumpe durch die ankommenden Blasen. Der Nachteil dabei: der Einsatz von viel Material macht die zu bewegenden Teile schwer, und es wird mehr Treibstoff benötigt.
Dank Smart Bubble System: leichtere Bauweise von Getriebeölpumpen mit weniger CO2-Ausstoß
Das in Osttirol federführend (im Verbund mit deutschen Projektpartnern) mitentwickelte Smart Bubble System diagnostiziert, wo und in welcher Verteilung Blasen auftauchen, wie sie sich verhalten und welche Auswirkungen sie auf die einzelnen Pumpen- und Getriebeteile haben. Mit den gewonnenen Erkenntnissen lassen sich Pumpenkonstruktionen gezielt optimieren, und es können leichtere und dünnere Materialien verbaut werden. Wird weniger Kraft benötigt, sinkt der für die Schmierung der beweglichen Getriebeteile benötigte Getriebeölverbrauch, was eine deutlich verbesserte
Energieeffizienz mit weniger CO2-Emissionen zur Folge hat.
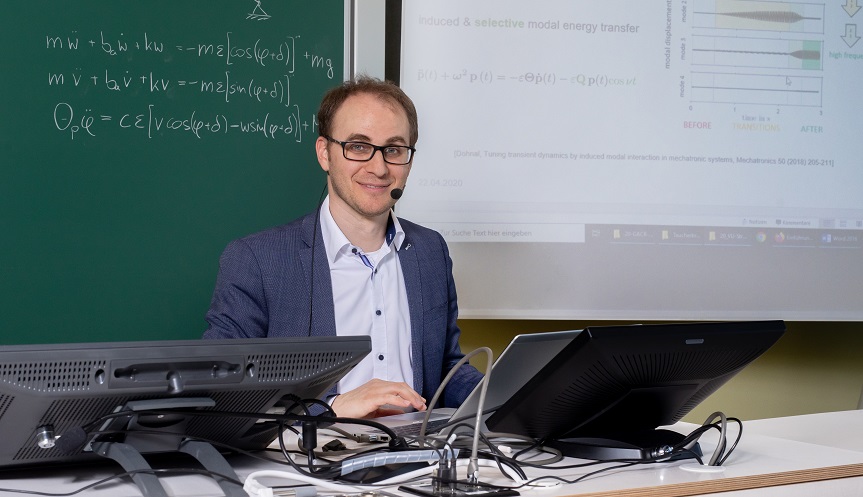
a.O. Unive.-Prof. DDI Dr. Fadi Dohnal: „Beim Kamerasystem und beim Herzstück des Systems – der Software für Bilderkennung haben zwei studentische Mitarbeiter – ein Doktorand und ein Bachelor-Student – entscheidende Arbeit geleistet.“
Große Nachfrage der Autozulieferindustrie – auch für E-Autos
Die Nachfrage nach einer Lösung der bislang ungelösten Luftblasen-Problematik ist auf Seiten der Autozulieferindustrie groß. „Der Markt für Getriebeölpumpen liegt aktuell bei ca. 100 Millionen Stück pro Jahr und steigt kontinuierlich“, erklärt Ing. Manuel Pölt, MAS, technischer Leiter bei testtec. Auch für E-Fahrzeuge bringt das Smart Bubble System eine entscheidende Verbesserung bei der Energieeffizienz, da auch sie Ölpumpen für Aktuierung, Schmierung und Kühlung benötigen: „In diesem Marktsegment gibt es noch höhere Anforderungen an die Pumpen und ihre Leistungsfähigkeit (Akustik, Verschleiß, Wirkungsgrad)“, so Pölt. Auch bei anderen Pumpen (z.B. Lenkpumpen) kann das System künftig zum Einsatz kommen.
Entwicklungskosten in Höhe von rund 700.000 Euro
Wie funktioniert das Smart Bubble System nun genau? „Am Prüfstand wird das Öl durch ein optimiertes Sichtfenster durchgequetscht. Beim Kamerasystem haben wir nicht auf ein bestehendes Modell zurückgegriffen, sondern alles von Grund auf selbst entwickelt. Dabei haben zwei studentische Mitarbeiter – ein Doktorand und ein Bachelor-Student – entscheidende Arbeit geleistet, so auch beim Herzstück des Systems selbst: der
Software für die Bilderkennung“, erklärt Mechatronik-Professor Dohnal den Entwicklungsprozess. Für die Entwicklung wurde ein Projektvolumen in Höhe von knapp 700.000 Euro aufgewendet – 50 Prozent der Finanzierung kamen über ein transnationales EU-Förderprojekt zustande.
Text: Redaktion, Fotos: Brunner Images